Demystifying Ball Bearings: How These Tiny Components Keep the World Moving
2025-03-11
Ball bearings might seem like small, insignificant parts, but they’re actually crucial for countless machines and devices we use every day. From the wheels on your car to the hard drive in your computer, ball bearings make smooth, efficient motion possible. This article will delve into the fascinating world of ball bearings, exploring their function, design, types, and applications. It’s worth reading because understanding these fundamental components can give you a greater appreciation for the engineering marvels around us and, for those in manufacturing and engineering, provide insights into selecting the right bearing for specific needs.
1. What Exactly is a Ball Bearing and Why is it So Important?
A ball bearing is a type of rolling-element bearing that uses balls to maintain the separation between the bearing races. The purpose of a ball bearing is to reduce friction between moving parts and facilitate smooth rotational movement. This reduction in friction translates to less energy consumption, reduced wear and tear, and increased efficiency in machinery. In essence, ball bearings are essential components that enable machines to operate smoothly and efficiently. They are literally the small parts that help the large parts do their jobs effectively, with less resistance and wasted energy. Because of their utility, ball bearings use is extremely widespread.
Imagine trying to spin a heavy wheel directly on an axle. The friction between the two surfaces would be immense, requiring significant force and generating a lot of heat. A ball bearing solves this problem by introducing small, hardened steel (or ceramic) balls between the moving parts. These balls roll rather than slide, dramatically reducing friction and allowing for much easier movement. They are indispensable in countless applications, making them one of the most widely bearings used in mechanical engineering.
2. How Do Ball Bearings Reduce Friction?
The key to understanding how ball bearings reduce friction lies in the difference between sliding friction and rolling friction. Sliding friction occurs when two surfaces rub directly against each other. This generates considerable resistance and heat. Rolling friction, on the other hand, occurs when a round object (like a ball) rolls across a surface. The contact area is much smaller, and the deformation of the ball and the surface it rolls on is the primary source of resistance. This rolling motion drastically reduce friction between moving parts.
The coefficient of friction for rolling motion is significantly lower than that for sliding motion. This is why it’s much easier to push a heavy object on wheels than to drag it across the floor. Ball bearings cleverly exploit this principle. By placing balls between the moving parts (inner and outer races), they replace sliding friction with rolling friction. This is a fundamental reason why ball bearings are used so extensively in machines. They provide a smooth, almost effortless, rotation that would otherwise be impossible.
The precisely manufactured balls and bearing races create an extremely efficient system for transferring motion.
3. What are the Main Components of a Ball Bearing?
A typical ball bearing consists of four main parts:
- Outer Ring (Outer Race): This is the stationary outer ring that typically fits into a housing.
- Inner Ring (Inner Race): This is the inner ring that typically fits onto a rotating shaft.
- Balls: These are the precisely manufactured spherical elements that roll between the inner and outer races. They are responsible for the primary function of reducing friction. These bearing balls are typically made of hardened steel, but can also be ceramic for certain applications.
- Cage (Retainer): This component separates the balls, maintaining even spacing and preventing them from rubbing against each other. This helps to further reduce friction and heat generation, and ensures smooth operation.
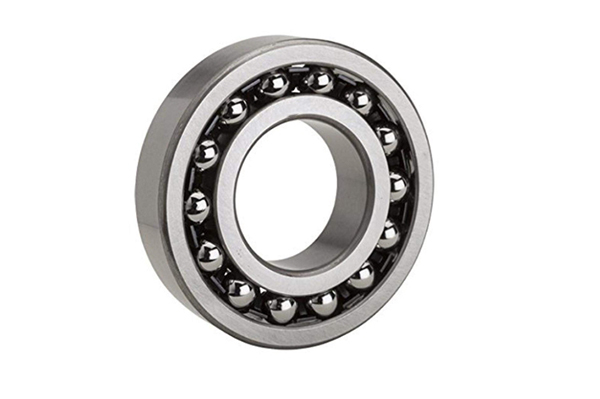
The inner and outer rings have grooves, called raceways, that are precisely shaped to match the curvature of the balls. These raceways guide the balls and ensure they roll smoothly. The design of the raceways also determines the types of loads the bearing can handle (radial, axial, or a combination). The whole assembly is a carefully engineered system designed for precision, durability, and efficiency.
4. What are the Different Types of Ball Bearings?
There are several different types of ball bearings, each designed for specific applications and load conditions. Here are some of the most common:
- Deep Groove Ball Bearings: These are the most common type of ball bearing. They are versatile and can handle both radial and moderate axial loads. Deep groove ball bearings are used in a wide variety of applications, from electric motors to gearboxes. They are known for their relatively simple design and cost-effectiveness.
- Angular Contact Ball Bearings: These bearings are designed to handle combined radial and axial loads, but primarily in one direction. Angular contact bearings have a contact angle that allows them to support significant axial forces. They are often used in pairs to handle loads in both directions.
- Self-Aligning Ball Bearings: These bearings have a spherical outer raceway, allowing them to accommodate some misalignment between the shaft and housing. Self-aligning ball bearings are ideal for applications where shaft deflection or mounting errors are expected.
- Thrust Ball Bearings: These bearings are designed to handle purely axial loads. Thrust ball bearings are not suitable for radial loads. They are commonly used in applications like automotive steering mechanisms.
- Single Row Ball Bearings: These bearings are known for their capacity to manage radial loads and limited axial loads efficiently.
- Double Row Ball Bearings: These bearings have a design featuring two rows of balls, providing higher load-carrying capacity and better resistance to misalignment compared to single-row bearings.
Xinda Slewing Bearing offers a wide selection of these bearing types, including Single Row -Ball Bearing Slewing Rings, suitable for various industrial needs.
5. How are Ball Bearings Manufactured?
The manufacturing of ball bearings is a highly precise process that requires specialized machinery and strict quality control. The process typically involves the following steps:
- Forming: The inner and outer rings are typically forged or machined from steel bars.
- Heat Treatment: The rings are hardened through a heat treatment process to achieve the required strength and durability.
- Grinding: The raceways on the inner and outer rings are precisely ground to the correct dimensions and surface finish. This is a critical step to ensure smooth rolling and low friction.
- Ball Production: The balls are made through a separate process involving heading, flashing, heat treatment, grinding, and lapping to achieve a highly spherical shape and precise dimensions.
- Assembly: The balls, inner and outer rings, and cage are assembled.
- Lubrication: The bearing is typically lubricated with grease or oil.
- Testing: The finished bearing undergoes rigorous testing to ensure it meets the required specifications for dimensional accuracy, running accuracy, and noise level.
Xinda Slewing Bearing, as a Factory specializing in the design and manufacture of slewing ring bearings, utilizes multiple production lines and advanced manufacturing techniques to ensure high-quality bearings.
6. What Materials are Used to Make Ball Bearings?
The most common material used in a wide range of ball bearings is high-carbon chromium steel (also known as bearing steel). This material offers a good balance of hardness, toughness, and wear resistance. However, other materials are also used, depending on the specific application requirements:
- Stainless Steel: Used in applications where corrosion resistance is critical, such as in food processing or marine environments.
- Ceramic (Silicon Nitride): Ceramic ball bearings offer several advantages over steel bearings, including higher speed capability, lower friction, longer life, and resistance to high temperatures. They are often used in demanding applications like machine tool spindles and aerospace applications.
- Hybrid Ball Bearings: uses ceramic balls and steel rings.
The choice of material significantly impacts the performance and life of ball bearings. For instance, bearings use ceramic balls in situations where extreme temperatures, high speeds, or corrosive environments are present.
7. What are the Key Considerations When Selecting a Ball Bearing?
Choosing the right ball bearing for a specific application is crucial for ensuring optimal performance and longevity. Key factors to consider include:
- Load Capacity: The bearing must be able to handle the expected radial and axial loads. The capacity of the bearings is a major design consideration.
- Speed: The bearing must be rated for the operating speed of the application.
- Operating Environment: Consider factors like temperature, humidity, and the presence of contaminants.
- Precision: Some applications require high-precision bearings, while others can tolerate lower precision.
- Stiffness: The stiffness of the bearing can affect the overall rigidity of the system.
- Life Expectancy: The required service life of the bearing should be considered.
- Size and Mounting: The bearing must fit within the available space and be compatible with the mounting arrangement. The width of the bearing is also a critical dimensional parameter.
By carefully evaluating these factors, engineers can select the most appropriate ball bearing designs for their specific needs. For instance, Precision double-row ball slewing ring would be a suitable choice for applications requiring high precision and load-carrying capacity.
8. Where are Ball Bearings Used? Exploring Common Applications.
Ball bearings are incredibly versatile and are used in a vast array of applications. Here are just a few examples:
- Automotive: Wheel bearings, transmissions, steering systems, engines.
- Industrial Machinery: Electric motors, pumps, gearboxes, conveyors, machine tools.
- Aerospace: Aircraft engines, control systems, landing gear.
- Household Appliances: Washing machines, refrigerators, vacuum cleaners, fans.
- Medical Equipment: CT scanners, MRI machines, dental drills.
- Robotics: Joints and actuators.
- Computer Hardware: Hard drives, cooling fans.
- Wind Turbines: Xinda Slewing Bearing supplies specialized bearings for demanding wind turbine applications, ensuring reliability and long service life.
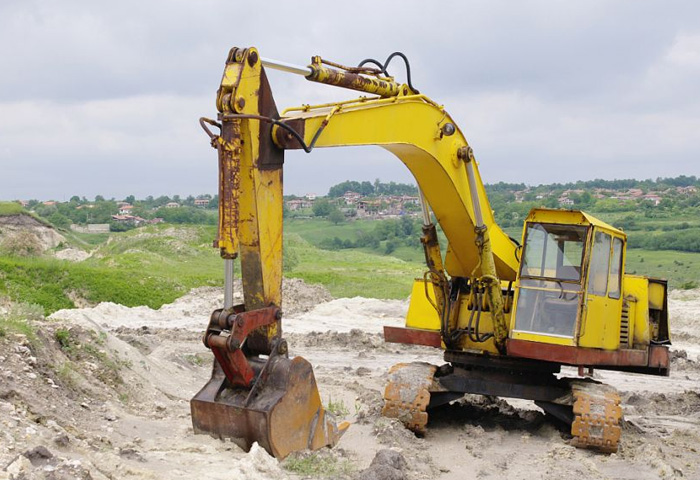
This list is far from exhaustive, demonstrating the ubiquitous nature of these critical components. The range of ball bearings find applications in is truly astounding. They really do keep much of the world turning!
9. How Does a Ball Bearing Failure Impact Machinery?
A ball bearing failure can have significant consequences, ranging from minor inconvenience to catastrophic equipment damage. Common causes of failure include:
- Overloading: Exceeding the bearing’s load capacity.
- Contamination: Dirt, dust, or other foreign particles entering the bearing.
- Improper Lubrication: Insufficient or incorrect lubrication.
- Fatigue: Repeated stress cycles eventually leading to material failure.
- Corrosion: Degradation of the bearing material due to chemical attack.
- Misalignment: Improper mounting or shaft deflection.
A failing bearing often exhibits symptoms like increased noise, vibration, and heat. If left unaddressed, the failure can lead to:
- Reduced Efficiency: Increased friction and energy loss.
- Equipment Damage: Damage to other components connected to the bearing.
- Downtime: Costly production stoppages.
- Safety Hazards: In some cases, a catastrophic bearing failure can pose a safety risk.
Regular inspection, proper lubrication, and timely replacement of worn bearings are crucial for preventing failures and ensuring the smooth operation of machinery.
10. What’s the Future of Ball Bearing Technology?
Ball bearing technology continues to evolve, with ongoing research and development focused on:
- Advanced Materials: Exploring new materials, such as advanced ceramics and coatings, to improve performance and durability.
- Smart Bearings: Integrating sensors into bearings to monitor their condition and predict failures.
- Improved Lubrication: Developing more effective lubricants and lubrication systems.
- Higher Precision: Achieving even tighter tolerances and smoother operation.
- Miniaturization: Developing smaller and more compact bearings for emerging applications.
- Increased Load Capacity: Improving load handling to meet the demands of new technologies.
These advancements will continue to enhance the performance, reliability, and efficiency of ball bearings, ensuring their continued importance in a wide range of industries. For example, the use of advanced coatings is helping to further reduce friction and wear, extending the life of ball bearings in demanding applications.
Summary: Key Takeaways
- Ball bearings are essential components that reduce friction between moving parts, enabling smooth and efficient rotational movement.
- They consist of an outer ring, inner ring, balls, and a cage.
- There are various types of ball bearings, each designed for specific load conditions and applications, such as I.1166.20.00.B Ball Slewing Bearing.
- Ball bearings are manufactured through a highly precise process involving forming, heat treatment, grinding, and assembly.
- The most common material is high-carbon chromium steel, but stainless steel and ceramics are also used.
- Selecting the right ball bearing requires careful consideration of factors like load capacity, speed, operating environment, and precision.
- Ball bearings are used in a vast array of applications, from automobiles to aerospace.
- Slewing converter,welding arms and positioning,light machines bearing utilize specialized bearings for precise control and positioning.
- Bearing failure can have significant consequences, highlighting the importance of proper maintenance.
- Ball bearings are also critical components in heavy equipment, such as the I.2025.50.15.D.1-R roller slewing bearing for bucket-wheel excavatorswheeled cranes.
- Ball bearing technology continues to evolve, with ongoing advancements in materials, sensors, and lubrication.