Flange Ball Bearings: The Ultimate Guide for Industrial Applications
2025-03-18
This article provides a comprehensive guide to flange ball bearings, explaining their design, functionality, applications, and benefits. For anyone involved in procurement, engineering, or manufacturing, understanding the nuances of flange bearings is crucial for selecting the right components for optimized machinery performance and longevity. This article is worth reading because it offers practical, real-world insights from a Chinese manufacturer’s perspective, addressing common pain points and key considerations for buyers, especially those sourcing globally.
What is a Flange Bearing and How Does it Work?
A flange bearing is a type of bearing designed to be mounted onto a surface perpendicular to the shaft axis. The defining feature of a flange bearing is the presence of a flange, or protruding rim, on the outer ring of the bearing. This flange design provides a secure and precise method of locating the bearing and preventing axial movement. The flange itself typically has bolt holes, allowing it to be easily fastened to a supporting structure, which can be part of housing or a machine frame.
Flange bearings can incorporate various types of bearing elements, including ball bearings, roller bearings, and plain bearings. The specific bearing type chosen depends on the load requirements, speed, and operating conditions of the application. The flange ensures precise alignment and simplifies the mounting process, making flange bearings a popular choice in many industrial applications. These bearings play a crucial role in reducing friction and enabling smooth rotational movement in a wide range of applications.
What are the Different Types of Flange Bearings Available?
Flange bearings come in various configurations to meet the diverse needs of different applications. Some common types include:
- Single Row Ball Flange Bearings: These are the most common type, utilizing a single row of steel balls to handle both radial and axial loads. They are suitable for moderate loads and speeds. Precision double-row ball slewing ring can be use.
- Single Row Roller Flange Bearings: Single-row roller flange bearings offer high load distribution capacity and high stiffnes. I.2025.50.15.D.1-R roller slewing bearing for bucket-wheel excavators,wheeled cranes is a great option.
- Double Row Ball Flange Bearings: Featuring two rows of balls, these bearings offer increased radial load capacity compared to single-row versions.
- Three Row Roller Flange Bearings: Designed for extremely heavy loads and demanding applications, these bearings provide exceptional rigidity and load-carrying capability.
- Light Type & Flange Slewing Ring Bearings: These are specialized flange bearings used in applications where large diameters and relatively light loads are involved, such as turntables and rotary tables.
- Flange Mounted Units: These consist of a bearing pre-mounted within a housing, simplifying installation and often incorporating seals for added protection. Pillow block units are a common example.
The choice between these various types depends on factors such as load, speed, alignment requirements, and environmental conditions. Bearing manufacturers offer a variety of materials and configurations to suit specific requirements.
What are the Key Advantages of Using Flange Bearings?
Flange bearings offer several significant advantages, making them a preferred choice in many applications:
- Simplified Mounting: The flange provides a built-in mounting surface, eliminating the need for separate mounting brackets or complex machining of the housing. This feature is particularly useful.
- Precise Alignment: The flange helps ensure accurate bearing alignment, minimizing misalignment issues that can lead to premature wear and failure. The flange ensures stability.
- Axial Load Support: The flange, when properly bolted, prevents axial movement of the bearing, providing support against thrust loads.
- Compact Design: Flange bearing units often have a compact footprint, saving space in machine designs.
- Ease of Replacement: When it’s time for maintenance or bearing replacement, flange bearings can be easily removed and replaced, minimizing downtime.
- Versatility: Flange bearings are available in various materials, sizes, and configurations, make them ideal for a wide range of applications.
- Provide stability: Flange bearings provide stability and reduce the possibility of displacement.
These advantages contribute to increased reliability, reduced maintenance costs, and improved overall machine performance. The secure mounting and precise alignment are particularly beneficial in applications involving high speeds or heavy loads.
How Do I Choose the Right Flange Bearing for My Application?
Selecting the correct flange bearing is critical for ensuring optimal performance and longevity. Several factors need to be considered:
- Load Capacity: Determine the radial and axial loads the bearing will need to support. Bearings are rated for specific load capacities, and exceeding these limits can lead to premature failure.
- Speed Requirements: Consider the operating speed of the shaft. High-speed applications may require bearings with specific features, such as precision balancing or specialized lubrication.
- Shaft Size: The bearing’s inner diameter must match the shaft diameter.
- Mounting Configuration: Choose a flange configuration (e.g., two-bolt, three-bolt, four-bolt) that is compatible with the supporting structure.
- Environmental Conditions: Consider factors such as temperature, humidity, and exposure to contaminants. Stainless steel bearings or sealed units may be necessary in harsh environments to prevent corrosion.
- Lubrication Requirements: Determine the appropriate lubrication method (grease or oil) and frequency based on the operating conditions.
- Specific Application Requirements: Consider any unique demands of the application, such as the need for low friction, high precision, or resistance to specific chemicals.
It’s essential to consider all these factors and consult with bearing manufacturers or application engineers to ensure the selected flange bearing meets the specific application requirements.
What are the Common Applications of Flange Bearings in Various Industries?
Flange bearings are commonly used in a wide range of industries due to their versatility and reliability. Some typical applications include:
- Construction Equipment: Cranes, excavators, and aerial platforms rely on flange bearings for smooth and reliable rotation.
- Wind Turbines: Large slewing flange bearings are used in the yaw and pitch systems of wind turbines.
- Conveyor Technology: Used to support rotating shafts in conveyor systems.
- Agricultural Machinery: Used in various rotating components of tractors, harvesters, and other equipment.
- Medical Equipment: CT scanners and MRI machines utilize precision flange bearings for smooth and quiet operation.
- Robotics: Flange bearings provide precise rotational movement in robotic arms and joints.
- Radar and Antenna Systems: Used for smooth and accurate rotation of antennas.
- Forestry Equipment: Flange bearings are used in heavy-duty machinery like log loaders and harvesters.
- Port Machinery: Cranes and other material handling equipment at ports utilize flange bearings.
- Automotive industry: Flange bearings find their way in transmission systems.
This list represents just a fraction of the applications where flange bearings play a vital role. They are used in various mechanical systems requiring rotational movement with secure mounting and precise alignment. Bearings are used wherever there is a need for reliable and efficient rotational motion.
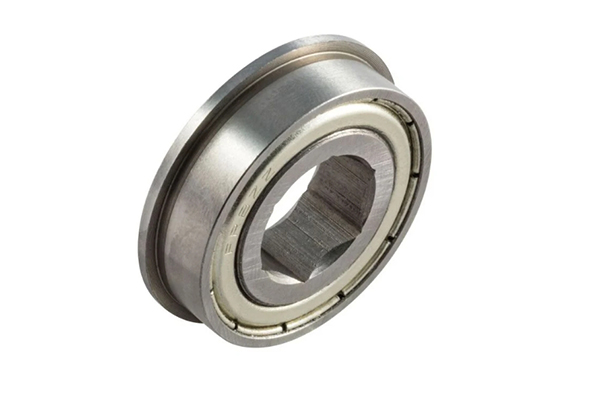
How to Ensure Proper Installation and Mounting of Flange Bearings?
Correct installation is crucial for maximizing the lifespan and performance of flange bearings. Here are some key steps:
- Surface Preparation: Ensure the mounting surface is clean, flat, and free of any debris or burrs.
- Alignment: Carefully align the bearing with the shaft and the mounting surface. Use shims if necessary to achieve precise alignment.
- Bolt Tightening: Use the correct torque specifications to tighten the mounting bolts. Over-tightening can damage the flange or the bearing, while under-tightening can lead to looseness and vibration.
- Shaft Securing: Secure to the shaft using set screws, locking collars, or other appropriate methods. Ensure the shaft is properly supported and aligned.
- Lubrication: Apply the correct type and amount of lubrication before operating the bearing.
- Initial Operation: After installation, run the bearing at a low speed and load to check for any unusual noise, vibration, or overheating.
Following these steps will help ensure a smooth and trouble-free operation. Proper mounting is essential for preventing premature wear and maximizing the bearing’s service life.
What is the Importance of Lubrication in Flange Bearing Performance?
Lubrication is absolutely critical to the performance and longevity of flange bearings. It serves several vital functions:
- Reduces Friction: Lubrication creates a thin film between the rolling elements and raceways, minimizing friction and wear.
- Dissipates Heat: Lubrication helps to carry away heat generated by the bearing’s operation, preventing overheating.
- Prevents Corrosion: Lubrication acts as a barrier against moisture and other contaminants, protecting the bearing from corrosion.
- Reduces Noise: Proper lubrication helps to dampen noise and vibration.
The type of lubrication (grease or oil) and the frequency of re-lubrication depend on the operating conditions, including speed, load, temperature, and environmental conditions. Using the correct lubrication and maintaining a proper lubrication schedule is essential for achieving optimal bearing performance and extending its service life.
Addressing Common Pain Points When Sourcing Flange Bearings.
Mark Thompson, a typical customer in the USA, often faces challenges when sourcing flange bearings from overseas suppliers. These pain points, and their solutions, are:
- Inefficient Communication: Language barriers and time zone differences can hinder communication with sales representatives.
- Solution: Xinda Slewing Bearing employs multilingual sales staff proficient in English, ensuring clear and prompt communication. We also offer flexible communication channels, including email and video conferencing, to accommodate different time zones.
- Shipment Delays: Delays in production or shipping can disrupt production schedules.
- Solution: Xinda Slewing Bearing maintains efficient production lines and strong relationships with reliable logistics partners. We provide regular updates on order status and proactively address any potential delays.
- Quality Issues: Bearings may not meet specified load requirements or dimensional tolerances.
- Solution: Xinda Slewing Bearing implements rigorous quality control procedures throughout the manufacturing process. We provide material certifications and dimensional accuracy reports, and our bearings comply with industry standards (e.g., ISO). We are committed to delivering high-quality products that meet or exceed customer expectations.
- Lack of Technical Support: Difficulty in obtaining technical assistance for specific application needs.
- Solution: Offer dedicated technical support teams to assist with bearing selection, application engineering, and troubleshooting.
Addressing these pain points directly builds trust and fosters long-term relationships with customers like Mark.
What Material Options are Available for Flange Bearings?
Flange bearings are available in various materials to suit different operating environments and performance requirements. Common materials include:
- Stainless Steel: Offers excellent corrosion resistance, making it suitable for use in harsh environments, such as food processing or marine applications.
- Chrome Steel: A common and cost-effective material providing good strength and durability.
- Cast Iron: Used for bearing housing in many applications, offering good strength and damping properties.
- Thermoplastic Housing: Lightweight and corrosion-resistant, often used in applications where weight is a concern.
- Plastic housing: Offers a lightweight and often self-lubricating option for lower-load applications.
The choice of material depends on factors such as load, speed, temperature, and exposure to corrosive substances. Selecting the appropriate material ensures the bearing can withstand heavy loads, and environmental challenging environments and provide long-lasting performance.
Understanding Load Capacity and Specifications for Flange Bearings.
Load capacity is a critical specification for flange bearings. It refers to the maximum radial and axial loads the bearing can handle without experiencing premature failure. Bearing manufacturers provide load ratings based on extensive testing and calculations. Key specifications to consider include:
- Static Load Rating: The maximum load the bearing can withstand when stationary.
- Dynamic Load Rating: The maximum load the bearing can withstand while rotating.
- Speed Limit: The maximum rotational speed the bearing can handle under specified load conditions.
- Dimensional Tolerances: The allowable variations in the bearing’s dimensions, which are crucial for proper fit and alignment.
- Material Specifications: Details on the materials used in the bearing‘s construction, including the type of steel and any coatings or treatments.
Understanding these specifications is essential for selecting a flange bearing that can safely and reliably handle the demands of the application. Exceeding the load capacity or speed limit can lead to bearing failure, potentially causing damage to the machinery and creating safety hazards.
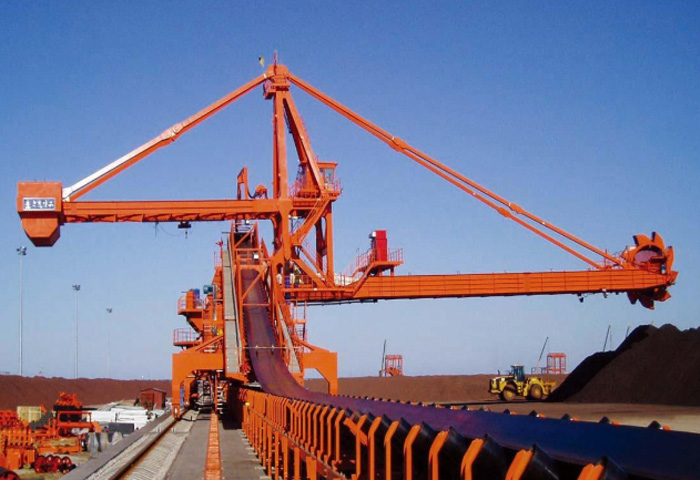
Why Choose a Chinese Manufacturer for Your Flange Bearing Needs?
Choosing a Chinese manufacturer like Xinda Slewing Bearing offers several advantages:
- Competitive Pricing: Chinese manufacturers often offer competitive pricing due to lower labor costs and economies of scale.
- High-Quality Manufacturing: Xinda Slewing Bearing, for example, utilizes advanced manufacturing technologies and rigorous quality control processes to produce high-quality bearings.
- Customization Capabilities: We can provide customized flange bearings to meet specific application requirements, including non-standard bearings sizes, materials, and configurations.
- Wide Product Range: We offer a wide range of flange bearing types and sizes, catering to diverse industry needs.
- Experience and Expertise: With years of experience in bearing design and manufacturing, we possess the expertise to deliver reliable and high-performance solutions.
- Strong Supply Chain: China has a well-developed industrial infrastructure and supply chain, ensuring a stable supply of raw materials and components.
By partnering with a reputable Chinese manufacturer, customers like Mark Thompson can benefit from cost-effective solutions without compromising on quality or reliability. We actively participate in industry exhibitions, providing opportunities for direct engagement and product evaluation.
Summary: Key Takeaways on Flange Bearings
- Flange bearings offer simplified mounting, precise alignment, and axial load support.
- Various types of flange bearings are available, including ball, roller, and slewing ring versions.
- Choosing the right flange bearing requires careful consideration of load, speed, shaft size, mounting configuration, and environmental conditions.
- Proper installation and lubrication are crucial for maximizing bearing performance and lifespan.
- Chinese manufacturers like Xinda Slewing Bearing offer competitive pricing, high-quality manufacturing, and customization capabilities.
- Addressing common pain points, such as communication barriers and quality concerns, is essential for building trust with international customers.
- Understanding load capacity and other specifications is crucial for selecting the correct bearing for the application.
- Flange bearings can be secured to the mounting surface using bolts.
- Flange bearings offer providing smooth and efficient operation.
By understanding these key points, engineers and procurement professionals can make informed decisions when selecting and using flange bearings, ensuring optimal performance and reliability in their machinery.