Torque in the context of a slewing ring bearing refers to the rotational force that must be applied to move or rotate the bearing under a given load. The calculation of torque is essential to determine the power requirements of the drive system and to ensure that the bearing can handle the loads and forces exerted on it.
The torque required for a slewing ring bearing depends on several factors, including the load applied, the coefficient of friction, the diameter of the bearing, and the speed of rotation. Let’s break down these factors and how they contribute to the overall torque calculation.
Key Factors in Slewing Ring Bearing Calculation
- Applied Load (Axial, Radial, and Moment Loads)
- Axial Load (F_a): This is the load applied parallel to the axis of rotation. Axial loads can significantly impact the torque required, especially if the load is large and concentrated in one area.
- Radial Load (F_r): This load is applied perpendicular to the axis of rotation and affects the bearing’s ability to rotate smoothly.
- Moment Load (M): This is the torque generated by a force acting at a distance from the axis of rotation. It is crucial for applications like cranes where loads are often offset from the center.
- Coefficient of Friction (μ)
The coefficient of friction between the bearing surfaces is a crucial factor in calculating torque. A higher coefficient of friction means more resistance to movement, resulting in higher torque requirements. The coefficient of friction depends on the materials used in the bearing and the lubrication conditions.
- Bearing Diameter (D)
The diameter of the slewing ring bearing plays a significant role in torque calculation. Larger diameters generally require more torque to rotate, as the distance from the center to the point of application increases. The diameter is typically measured as the mean diameter between the inner and outer raceways.
- Rotational Speed
While rotational speed is more directly related to the power requirements of the drive system, it can also influence the torque calculation. Higher speeds may require adjustments to the torque calculation to account for dynamic forces and potential increases in friction.
The Basic Torque Calculation Formula
The torque (T) required for a slewing ring bearing can be estimated using a simplified formula that incorporates the key factors mentioned above:
T=(Fa×μ×D)+MT = (F_a \times \mu \times D) + MT=(Fa×μ×D)+M
Where:
- TTT = Torque (Nm)
- FaF_aFa = Axial load (N)
- μ\muμ = Coefficient of friction
- DDD = Mean diameter of the bearing (m)
- MMM = Moment load (Nm)
This formula assumes that the radial load is relatively small compared to the axial and moment loads. In cases where the radial load is significant, additional calculations may be needed to account for its impact on the overall torque.
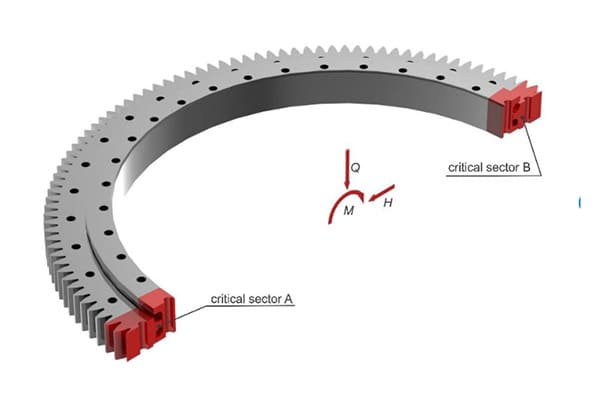
Practical Considerations
- Load Distribution: In real-world applications, loads may not be uniformly distributed across the bearing. Uneven load distribution can lead to higher localized forces, requiring a more detailed analysis to accurately calculate the torque.
- Lubrication: Proper lubrication can significantly reduce the coefficient of friction, thereby lowering the torque required. It’s important to consider the type and quality of lubrication used when performing slewing ring-bearing calculations.
- Safety Factors: To ensure reliability and prevent failure, engineers often apply safety factors to their torque calculations. This accounts for potential variations in loads, environmental conditions, and material properties.
- Dynamic Loads: If the application involves dynamic or fluctuating loads, such as in rotating cranes or wind turbines, it’s essential to consider these factors in the torque calculation. Dynamic loads can increase the stress on the bearing and require more torque to maintain smooth operation.
Conclusion
Calculating the torque for a slewing ring bearing is a critical step in the design and operation of rotating machinery. By considering factors such as applied loads, the coefficient of friction, bearing diameter, and rotational speed, engineers can determine the torque required to ensure smooth and efficient operation. Proper torque calculation helps in selecting the appropriate drive system and ensures the longevity and reliability of the bearing, which is essential in heavy-duty applications.