How to Choose the Right Slewing Ring Type?
2024-09-10
Slewing rings, also known as slewing bearings, play a critical role in a wide range of heavy-duty applications, from cranes and excavators to wind turbines and industrial machinery. These large, robust bearings are designed to handle axial, radial, and tilting moment loads, making them essential components in equipment that requires smooth and precise rotational movement. However, choosing the right slewing ring type for your specific application can be a complex task. This article will guide you through the key factors to consider when selecting the appropriate slewing ring for your needs.
Slewing rings come in various types, each designed to meet specific operational requirements. The most common types include:
- Single-Row Four-Point Contact Ball Bearings: These slewing rings are versatile and can accommodate axial, radial, and tilting moment loads. They are widely used in applications like cranes, where precise and smooth rotation is critical.
- Double-Row Angular Contact Ball Bearings: Offering higher load-carrying capacity, these bearings are suitable for applications with heavier axial loads, such as in wind turbines and large excavators.
- Crossed Roller Bearings: Known for their ability to handle higher radial loads and tilting moments, crossed roller bearings are ideal for applications requiring high rigidity and accuracy, such as in robotics and medical equipment.
- Three-Row Roller Bearings: These bearings are designed for heavy-duty applications where high load capacity is required. The three rows of rollers allow for the separate handling of axial, radial, and tilting moment loads, making them suitable for large cranes and mining equipment.
- Lightweight Slewing Rings: For applications where weight is a concern, such as in aerospace or small machinery, lightweight slewing rings made from specialized materials provide the necessary performance without adding excessive weight.
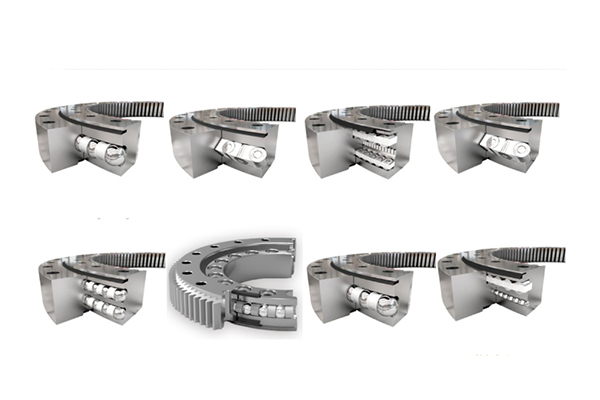
Factors to Consider When Choosing a Slewing Ring
When selecting a slewing ring, it’s essential to evaluate the specific needs of your application to ensure optimal performance and longevity. Here are the key factors to consider:
- Load Requirements:
- Axial Load: This is the load acting along the axis of rotation. Applications with significant axial loads, such as cranes and wind turbines, require slewing rings with high axial load capacity.
- Radial Load: The load perpendicular to the axis of rotation. Heavy radial loads are common in applications like rotating platforms and industrial robots.
- Tilting Moment Load: The load that creates a moment about the axis of rotation, often seen in applications with cantilevered loads, such as excavators.
Understanding the specific load conditions in your application will help determine the type and size of the slewing ring needed.
- Rotational Speed:
- Different slewing rings are designed to operate at different speeds. For high-speed applications, such as in wind turbines or rotating machinery, choosing a slewing ring with low friction and appropriate lubrication is crucial to prevent overheating and wear.
- Precision Requirements:
- Applications like robotics and medical devices demand high precision in rotational movement. Crossed roller bearings, known for their accuracy and rigidity, are often the best choice for these applications.
- Environmental Conditions:
- The operating environment plays a significant role in selecting a slewing ring. For harsh conditions, such as in marine or mining environments, it’s essential to choose a slewing ring with appropriate sealing and corrosion-resistant materials to withstand exposure to moisture, dust, and chemicals.
- Installation Space:
- The available space for installation will influence the size and type of slewing ring you can use. Compact applications may require lightweight or low-profile slewing rings, while larger installations can accommodate more substantial designs.
- Maintenance Requirements:
- Some slewing rings require regular maintenance to ensure longevity, while others are designed for minimal maintenance. Understanding your maintenance capabilities and requirements will help in choosing the right bearing.
Consulting with Experts
Given the complexity of selecting the appropriate slewing ring, it’s often beneficial to consult with experts or the manufacturer. They can provide detailed recommendations based on your specific application requirements, ensuring that you choose a slewing ring that meets all operational needs.
Conclusion
Choosing the right slewing ring type is critical for ensuring the efficient and reliable operation of your equipment. By carefully considering factors such as load requirements, rotational speed, precision, environmental conditions, installation space, and maintenance needs, you can select a slewing ring that will provide optimal performance and durability. Whether you are working in construction, manufacturing, or renewable energy, the right slewing ring will contribute significantly to the success of your project.