Unlocking Maximum Load Capacity: The Power of Three-Row Roller Slewing Ring Bearings
2025-04-08
Three-row roller slewing bearings represent the pinnacle of load-carrying capability within the slewing ring family. Designed for the most demanding applications, these robust components utilize three independent rows of cylindrical rollers to handle immense axial, radial, and tilting moment loads simultaneously. Understanding the design, advantages, and applications of the three-row roller bearing is crucial for engineers and procurement specialists like Mark Thompson, who need reliable, high-capacity solutions for heavy machinery. This article delves into the specifics of three-row roller slewing ring technology, exploring why it’s often the preferred choice for equipment like heavy-duty cranes, excavators, and stacker reclaimers, and how partnering with an experienced bearing manufacturer like Xinda Slewing Bearing ensures you get the right product for your needs. We’ll cover the fundamental mechanics, comparative advantages, selection criteria, and the critical role of quality control in delivering dependable long service life.
What Exactly is a Three-Row Roller Slewing Bearing?
A three-row roller slewing bearing, sometimes referred to as a three-row cylindrical roller slewing ring, is a large-diameter bearing engineered for maximum load capacity. As the name suggests, the defining characteristic of this bearing type is its three distinct rows of rolling elements. These are typically cylindrical rollers, chosen for their ability to handle high loads compared to balls. The slewing bearing has three rings: an inner ring, an outer ring, and often segmented rings that form the raceways.
Unlike simpler bearing designs where a single set of rolling elements handles all load types, the three-row roller bearing segregates these forces. One row is dedicated primarily to handling radial loads, while the other two rows are oriented to manage axial loads and the resulting tilting moments. This specialized arrangement allows the bearing to accommodate extremely high forces from multiple directions simultaneously, making it a go-to solution for heavy industrial machinery. The use of cylindrical rollers, often in a full complement cylindrical roller arrangement (meaning maximum number of rollers without a cage), further maximizes the contact area and thus the load carrying capacity.
The construction involves precision-machined inner and outer rings, typically featuring mounting holes for bolts and often incorporating integral gearing (internal or external). The rollers run in hardened raceways designed to withstand the intense pressures generated under heavy load. Seals are incorporated to protect the internal components from contamination and retain lubrication, crucial for achieving a long service life. This sophisticated design makes the three-row roller bearing a complex but highly effective component.
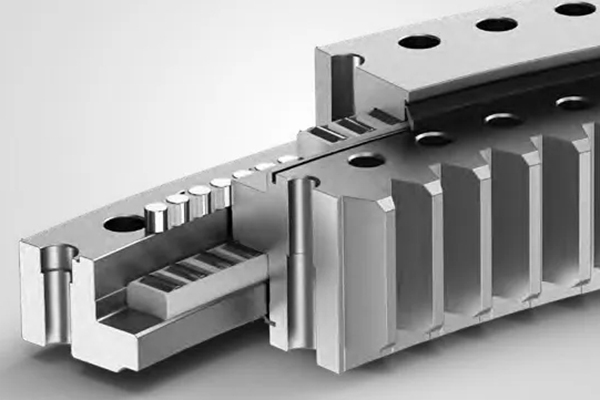
How Does the Unique Three-Row Design Distribute Load So Effectively?
The genius of the three-row roller bearing lies in its dedicated load paths. The axial and radial raceways are separated, allowing different rows of rollers to handle specific forces optimally. Typically, the arrangement works as follows:
- Radial Load: One row of cylindrical rollers is oriented horizontally (axis parallel to the bearing axis). This row primarily bears the radial loads – forces acting perpendicular to the shaft axis.
- Axial Load & Tilting Moment: Two rows of cylindrical rollers are oriented vertically (axis perpendicular to the bearing axis). These rollers can bear axial forces – loads acting parallel to the shaft axis – in both directions (upward and downward). Crucially, these two axial rows also work together to counteract the tilting moment load, which arises when forces are applied off-center, trying to tip the rotating structure. The separation distance between these two axial rows provides the leverage needed to resist these moments effectively.
This segregation means that the bearing doesn’t compromise its ability to handle one type of load when subjected to another. Each row of rollers can bear its designated force component efficiently. The combination of one radial row and two axial rows results in a bearing with exceptional carrying capacity for combined loads – axial, radial, and moment – simultaneously. The three-row roller slewing ring configuration provides very high stiffness and minimizes deflection under heavy operational loads, which is vital for maintaining positional accuracy in large machinery like a crane or excavator. The full complement cylindrical roller design in each row maximizes the number of load-carrying contact points.
This structural approach ensures that forces are distributed across a large number of rollers specifically designed and positioned for that force direction. The rollers can bear axial and radial loads respectively, leading to lower contact stresses on individual rollers and raceways compared to bearings where a single row handles everything. This distribution directly translates to higher overall load carrying potential and contributes significantly to the bearing‘s robustness and longevity under extreme conditions. It’s one of the four products (along with single row ball, single row roller, and double row ball) in the standard slewing ring family, but offers the highest capacity.
What are the Key Advantages of Using a Three-Row Roller Series?
The primary advantage of the three-row roller bearing series is its unparalleled load capacity. This makes it the default choice when dealing with extreme forces. Let’s break down the key benefits:
- Highest Load Capacity: Compared to single-row ball, single-row roller, or double-row ball slewing bearings, the three-row cylindrical roller design offers the maximum ability to carry combined axial loads, radial loads, and tilting moment loads. This is due to the specialized rows and the use of cylindrical rollers.
- High Stiffness: The multiple rows of rollers and their specific orientation provide exceptional structural rigidity. This minimizes deflection under load, ensuring precise movement and stability, which is critical for applications like large cranes and radar systems.
- Accommodation of Heavy Tilting Moments: The two axially oriented roller rows are spaced apart, creating a strong lever arm to resist the significant tilting moments common in applications like large excavators digging or heavy lift cranes handling offset loads.
- Durability and Long Service Life: By distributing loads effectively across dedicated roller rows, stress concentrations are reduced. Combined with robust materials and proper sealing, this leads to a longer operational lifespan even under continuous heavy-duty service.
- Suitable for Large Diameters: The design inherently scales well for large-diameter applications, where immense loads are the norm.
Comparison of Load Capacities (Illustrative):
Bearing Type |
Axial Capacity |
Radial Capacity |
Moment Capacity |
Stiffness |
---|
Single Row Ball |
Moderate |
Moderate |
Moderate |
Moderate |
Single Row Roller |
High |
High |
High |
High |
Double Row Ball |
High |
Moderate |
High |
High |
Three-Row Roller |
Very High |
Very High |
Very High |
Very High |
This table highlights why the three-row roller bearing stands out when maximum performance is required. While other series offer excellent performance for many applications, the three-row roller excels where loads push the limits. Our factory specializes in producing these high-capacity bearings, ensuring each product meets rigorous standards.
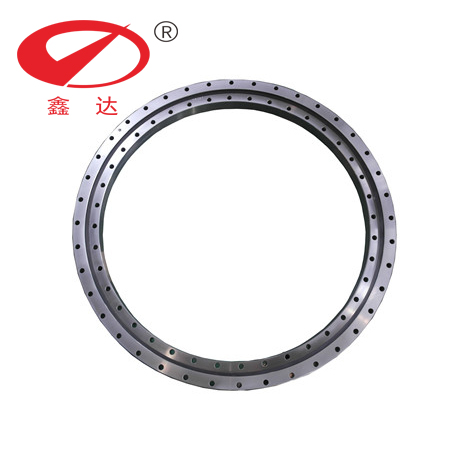
How Do Three-Row Roller Bearings Compare to Other Slewing Ring Types?
Choosing the right slewing bearing type involves understanding the trade-offs between different designs. Here’s a comparison focusing on the three-row roller bearing:
- vs. Single Row Four Point Contact Ball Bearings: Single row ball bearings are versatile and cost-effective for moderate loads. They use one row of balls in specially designed raceways to handle axial, radial, and moment loads. However, their point contact means lower load capacity and stiffness compared to the line contact of rollers in a three-row design. They are generally lighter and have lower friction. An example could be the E.1200.20.00.B BALL BEARING.
- vs. Single Row Crossed Roller Bearings: These use a single row of cylindrical rollers arranged orthogonally (crossed). They offer good stiffness and high load capacity for their size, handling all load types effectively. However, the three-row roller bearing typically surpasses them in ultimate load carrying capacity, especially for very high axial and moment loads, due to its dedicated roller rows.
- vs. Double Row Ball Bearings: These use two rows of balls, offering higher load capacity (especially axial and moment) than single-row ball bearings. They provide good stiffness. Still, the three-row roller bearing generally provides superior overall load capacity (axial, radial, and moment) and greater stiffness due to the use of three rows of cylindrical rollers and their optimized arrangement. An example of a double-row ball bearing is the 011.20.1220.000.11.1504 Precision double-row ball slewing ring.
- vs. Double Row Roller Bearings (Combined): Some designs combine roller types or orientations in two rows. While capable, the dedicated three–row structure usually achieves higher specific load ratings, particularly for the tilting moment.
In essence, the three-row roller bearing is the heavyweight champion. You choose it when the application loads exceed the capabilities of other slewing bearing types. The trade-off is typically higher cost, weight, and potentially slightly higher friction compared to ball bearings, but these are often secondary considerations when extreme load support is the primary requirement. Its complexity requires precise manufacturing, a service we excel at in our Luoyang facility.
Which Heavy-Duty Applications Demand the Strength of Three-Row Roller Slewing Rings?
The exceptional load-bearing characteristics of three-row roller slewing bearings make them indispensable in some of the world’s largest and most powerful rotating machinery. Their ability to handle massive combined loads reliably dictates their use in sectors where failure is not an option. Key application areas include:
- Heavy Lift Cranes: Mobile cranes, crawler cranes, truck cranes, offshore cranes, and ship cranes rely on these bearings for stable rotation under immense lifting loads and significant tilting moments. The high stiffness ensures precise crane control.
- Large Excavators and Mining Shovels: The digging forces and the weight of the boom and bucket generate enormous axial, radial, and moment loads, perfectly suited for the capacity of a three-row roller bearing. Think of bucket-wheel excavators or large hydraulic mining shovels. A relevant product example is the I.2025.50.15.D.1-R roller slewing bearing for bucket-wheel excavators,wheeled cranes.
- Stackers and Reclaimers: Used in bulk material handling at ports and mines, these massive machines require robust slewing bearings to support their long booms and handle the associated loads during operation.
- Tunnel Boring Machines (TBMs): The cutterhead drive and articulation systems of large TBMs operate under extreme forces, necessitating the use of high-capacity three-row roller bearings.
- Offshore Technology: Wind turbines (especially large offshore models), oil and gas platforms, and ship-mounted equipment often utilize these bearings due to the high dynamic loads imposed by wind, waves, and operational forces.
- Steel Mill Equipment: Ladle turrets and continuous casting machines handle molten metal, requiring bearings with high load capacity and reliability under harsh conditions.
- Large Radar and Telescope Mounts: The need for extremely high stiffness and precise pointing accuracy under significant weight and wind loads often leads to the selection of three-row roller bearings.
In each case, the common factor is the presence of very large static and dynamic loads, often acting in combination (axial, radial, moment). The three-row roller bearing provides the necessary support and rotational capability for these demanding scenarios, ensuring the machine operates safely and efficiently.
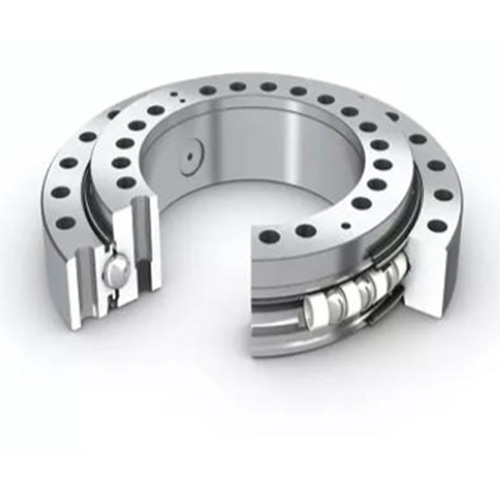
Understanding Gear Options: Internal vs. External Gears in Three-Row Roller Bearings?
Most three-row roller slewing bearings incorporate integral gearing on either the inner or outer ring to facilitate rotation via a pinion drive system. The choice between internal and external gearing depends on the specific machine design and operational requirements:
- External Gear:
- The gear teeth are cut on the outer diameter of the non-rotating ring (usually the inner ring in most heavy equipment like cranes or excavators, which mounts to the chassis).
- Pros: Easier access for pinion engagement and maintenance, potentially simpler pinion mounting.
- Cons: Gear teeth are exposed to the environment, requiring protection (shrouding) against debris and damage. Can increase the overall footprint of the drive system.
- Internal Gear:
- The gear teeth are cut on the inner diameter of the non-rotating ring (usually the outer ring in applications where it’s fixed).
- Pros: Offers inherent protection for gear teeth from external impact and contamination. Allows for a more compact drive arrangement as the pinion operates within the bearing’s diameter. Can sometimes offer a higher gear ratio potential for a given size.
- Cons: Pinion access and mounting can be more complex. Maintenance might require more disassembly.
Non-Geared:
- Some applications, particularly those driven by alternative means (e.g., hydraulic motors directly coupled, or large ring gears separate from the bearing) may utilize a three-row roller bearing without integral gears. This is less common for the primary slewing function in heavy machinery but possible for certain positioning tables or specialized equipment.
The choice impacts the overall design of the drive mechanism, including the motor, gearbox, and pinion mounting. Factors like required torque, speed, space constraints, environmental protection needs, and maintenance access influence the decision. As a bearing manufacturer, we produce three-row roller bearings in all three configurations (internal gear, external gear, and non-geared) based on customer specifications. The gear quality (tooth profile accuracy, hardness, finish) is as critical as the bearing performance itself, and subject to stringent quality control.
What Factors Influence the Selection of the Right Three-Row Roller Bearing Product?
Selecting the appropriate three-row roller bearing is critical for ensuring machinery performance, safety, and longevity. Procurement officers like Mark Thompson, often working with their engineering teams, need to consider several key factors:
- Load Spectrum: This is paramount. Accurately determining the maximum and typical operating loads is essential. This includes:
- Axial Load: Vertical forces (weight, lifting forces).
- Radial Load: Horizontal forces (side loads, wind loads).
- Tilting Moment Load: Forces acting at a distance, trying to tilt the structure.
The bearing‘s capacity ratings must comfortably exceed these operational loads with appropriate safety factors.
- Dimensions: The required diameter (bore, outside diameter) and height must match the available space and mounting structure of the machine. Bolt circle diameters and hole patterns are also critical for integration.
- Rotational Speed and Duty Cycle: While typically used in slow-rotating applications, the required speed and how continuously the bearing operates influence lubrication requirements and potential heat generation.
- Precision and Stiffness Requirements: Applications like radar or precision machining tables demand higher rotational accuracy and minimal deflection (high stiffness) compared to some bulk handling equipment. This affects manufacturing tolerances.
- Gearing Requirements: If geared, specify internal or external, the required module, number of teeth, gear quality standards, and material/hardness requirements for the gear and pinion combination.
- Sealing: The operating environment dictates the required sealing effectiveness. Harsh, dusty, or wet conditions necessitate robust sealing solutions to prevent contamination and retain grease.
- Material and Corrosion Protection: Standard bearing steel is common, but corrosive environments (marine, chemical) may require special materials or coatings for the rings, rollers, and fasteners. Material certifications are often required.
- Operating Temperature Range: Extreme temperatures can affect lubricant performance and material properties.
- Lead Time and Cost: While performance is key, project timelines and budget constraints are always factors. Balancing product specifications with delivery schedules and cost is crucial. Reliable lead times are a major concern for buyers like Mark.
As a bearing factory, we work closely with customers to understand these requirements and recommend or custom-design the optimal three-row roller bearing solution. Providing detailed technical specifications and load calculations helps ensure the selected product is perfectly matched to the application.
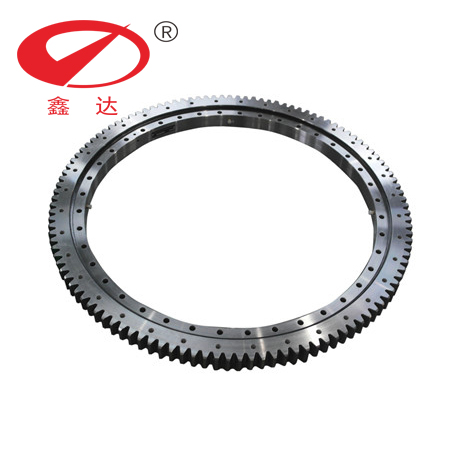
Why Choose a China-Based Manufacturer Like Xinda for Your Slewing Bearing Needs?
For buyers like Mark Thompson, sourcing components from China offers significant advantages, particularly when partnering with a reputable factory like Xinda Slewing Bearing. While cost-effectiveness is often a driver, the benefits extend far beyond price, especially in the complex bearing industry:
- Manufacturing Expertise: China, particularly regions like Luoyang, has become a global hub for bearing manufacturing. Decades of experience, investment in technology, and a skilled workforce allow factories like ours to produce complex products like three-row roller bearings to high standards.
- Competitive Pricing: Efficient production processes, economies of scale, and competitive labor markets allow Chinese manufacturers to offer highly competitive pricing without necessarily compromising quality, addressing Mark’s need for cost-effective solutions.
- Full Range Production: We offer a wide range of slewing bearings, from standard series to custom designs, including single row ball, single row roller, double row ball, and the high-capacity three-row roller bearings. This includes various sizes, gear types (internal, external, non-geared), and sealing options. Check our diverse offerings like the I.1166.20.00.B Ball Slewing Bearing.
- Customization Capabilities: Experienced factories possess strong engineering teams capable of designing and manufacturing bespoke slewing bearings tailored to specific customer requirements and unique applications.
- Direct Communication: Working directly with a factory like Xinda eliminates intermediaries, potentially reducing costs and improving communication clarity – addressing a key pain point Mark sometimes faces. We prioritize clear, responsive communication.
- Focus on Quality: Reputable manufacturers understand that long-term success depends on product quality. We invest heavily in quality control systems, testing equipment, and certifications (like ISO) to ensure our bearings meet international standards and customer expectations for load capacity and long service life.
While challenges like communication styles or managing logistics can exist, partnering with an established, professional bearing manufacturer in China mitigates these risks. Attending exhibitions is a great way to meet suppliers face-to-face, but thorough vetting through factory audits, reviewing certifications, and clear technical discussions are crucial. We pride ourselves on being a reliable partner, offering high-quality products, dependable service, and transparent processes.
What Quality Control Measures Ensure Reliable Performance in Three-Row Roller Bearings?
Ensuring the reliability and long service life of a three-row roller bearing, especially given the critical applications they serve, demands rigorous quality control throughout the manufacturing process. For a buyer concerned about meeting specifications, understanding these measures builds confidence:
- Raw Material Inspection: It starts with the steel. We verify material certifications for rings and rollers, ensuring they meet specified chemical composition, purity, and mechanical properties (hardness potential). Dimensional checks on raw forgings are also performed.
- In-Process Dimensional Control: Precision machining is critical. We use advanced CNC machines and regularly check critical dimensions like raceway profiles, diameters, concentricity, parallelism, and gear tooth geometry (if applicable) using Coordinate Measuring Machines (CMM) and specialized gauges. Tolerances for three-row roller bearings are often very tight.
- Heat Treatment Verification: The hardening of raceways and gear teeth is vital for wear resistance and load carrying capacity. We monitor furnace parameters and perform hardness testing (surface and core) to ensure the correct depth and hardness values are achieved consistently.
- Rolling Element Quality: Cylindrical rollers are sourced from reputable suppliers or manufactured in-house to strict standards. They undergo checks for dimensional accuracy, roundness, surface finish, and hardness. Full complement cylindrical roller sets require careful arrangement and inspection.
- Assembly Checks: Proper assembly is crucial. This includes verifying clearances (preload or clearance), ensuring correct roller placement, proper seal installation, and applying the initial grease fill. Rotational torque testing (no-load) is performed to check for smooth rotation.
- Final Inspection: Before shipment, each bearing undergoes a final comprehensive inspection. This includes visual checks, re-verification of key dimensions, confirmation of markings (part number, serial number), gear inspection (if applicable), and packaging checks to prevent damage during transit.
- Documentation and Traceability: Maintaining detailed records (material certs, inspection reports, test results) linked to each bearing‘s serial number ensures traceability and accountability. We provide necessary documentation to customers upon request.
These stringent measures, often aligned with ISO 9001 quality management systems, are designed to catch any deviations early and ensure that the final product delivered to customers like Mark meets or exceeds the specified performance requirements, particularly regarding load capacity, dimensional accuracy, and smooth operation. This commitment to product quality helps prevent the pain points associated with premature failure or non-conformance.
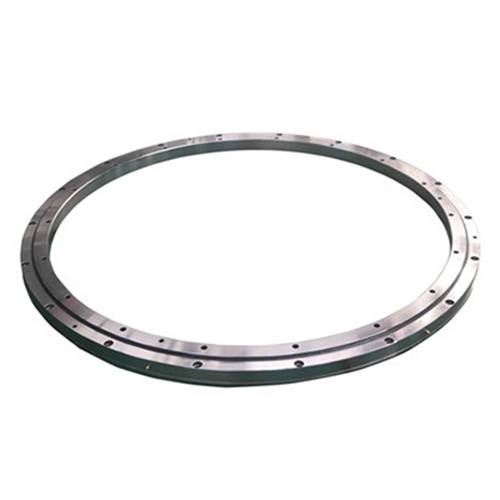
The Future Outlook for Three-Row Cylindrical Roller Slewing Bearings
The demand for three-row roller slewing bearings is closely tied to trends in heavy industry and large-scale infrastructure projects. As machinery continues to grow in size and capacity, the need for bearings capable of handling extreme loads will persist and likely increase.
- Larger Machinery: Trends in wind energy (larger turbines), mining (bigger shovels and excavators), and construction (higher capacity cranes) directly drive the need for larger diameter and higher capacity slewing bearings. The three-row roller bearing is well-positioned to meet these demands.
- Increased Precision: Even in heavy machinery, there’s a growing need for more precise control and positioning, demanding bearings with higher stiffness and lower runout – areas where three-row designs excel.
- Material and Design Innovations: Ongoing research focuses on improved steel alloys, advanced heat treatment techniques, optimized raceway geometries, and enhanced sealing solutions to further improve load capacity, durability, and service life under even harsher conditions. The development of specialized cylindrical roller bearings continues.
- Smart Bearings: Integration of sensors for monitoring temperature, vibration, and load in real-time is an emerging trend. This allows for predictive maintenance, reducing downtime in critical equipment, and could become more common even in large roller bearing types.
- Global Infrastructure Growth: Investments in infrastructure projects worldwide (ports, transportation, energy) will continue to fuel demand for the types of heavy equipment that rely on three-row roller bearings.
While representing the upper echelon of slewing bearing technology, the three-row roller design remains fundamental for applications where load capacity is the ultimate criterion. As a professional bearing manufacturer, we are committed to staying at the forefront of these developments, continually refining our design and manufacturing processes to deliver the robust, reliable slewing solutions our global customers require for their most challenging projects. The three-row cylindrical roller bearing will remain a cornerstone product in the heavy bearing market for the foreseeable future.
Key Takeaways:
- Highest Capacity: Three-row roller bearings offer the highest combined load (axial, radial, moment) carrying capacity among standard slewing bearing types due to their dedicated roller rows.
- Design Principle: They utilize three rows of cylindrical rollers, typically one horizontally oriented for radial loads and two vertically oriented for axial and moment loads.
- Key Advantages: Superior load capacity, high stiffness, excellent moment resistance, and long service life under heavy-duty conditions.
- Primary Applications: Essential for heavy lift cranes, large excavators, mining equipment, stackers/reclaimers, TBMs, offshore platforms, and other large-scale machinery.
- Configuration Options: Available with internal gears, external gears, or non-geared to suit drive system requirements.
- Selection Criteria: Based primarily on load spectrum, dimensions, stiffness needs, gearing, sealing, and operating environment.
- Quality is Crucial: Rigorous quality control, from material inspection to final testing, is vital for ensuring reliable performance and meeting specifications.
- Manufacturing Source: Reputable China-based factories like Xinda offer expertise, competitive pricing, customization, and a full range of slewing bearing products.