What is a Slewing Ring Drive?
2024-11-07
A slewing ring drive is a highly versatile component used in a wide range of industrial applications, particularly where rotational motion needs to be controlled with precision and stability. Essentially, a slewing ring drive is a type of gearbox that facilitates rotation or turning movement between two parts, generally supporting heavy loads and working under harsh conditions. These devices are invaluable in many fields, from construction and manufacturing to renewable energy, defense, and robotics. Here’s a deeper look into what a slewing ring drive is, how it works, and some of its main applications.
A slewing ring drive consists of a gear, usually housed in a casing, which is capable of rotating 360 degrees or performing partial rotations. The core of a slewing drive system is the slewing bearing, also known as a slewing ring, which provides smooth, reliable rotational movement under load. The slewing bearing combines both radial and axial bearings in a single unit, allowing it to support high loads both horizontally and vertically.
These drives typically use either a worm gear or a pinion gear system. In worm gear designs, a threaded shaft (the worm) engages with the teeth of a gear ring to create motion. This setup provides a high torque output and self-locking capability, making it particularly beneficial for applications requiring stability, like positioning systems and load-bearing turntables.
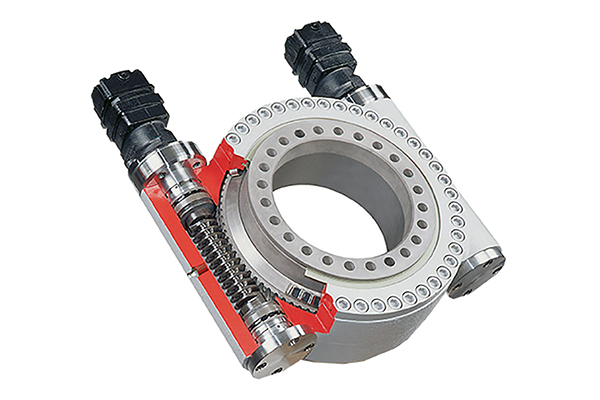
How Does a Slewing Ring Drive Work?
Slewing ring drives work by transferring power from an input (often an electric or hydraulic motor) through the worm or pinion gears, which in turn rotate the slewing ring. This controlled rotational movement allows the load to move smoothly and steadily in a circular or semi-circular motion. The simplicity of the design—combining a rotational element and a load-bearing structure in one—means fewer components, which often translates to higher reliability and reduced maintenance.
Key Advantages of Slewing Ring Drives
- High Load Capacity: Slewing ring drives are capable of handling significant loads, both axial (along the axis of rotation) and radial (perpendicular to the axis). This makes them well-suited for applications involving heavy-duty machinery.
- Compact Design: The integration of the slewing bearing and drive unit into one compact structure saves space and simplifies assembly. This compact design is advantageous in applications where space is limited but high performance is required.
- Precision and Control: Slewing drives allow precise control over rotational movement. Some designs, especially those using worm gears, also offer self-locking capabilities, which prevent the drive from moving when the motor isn’t engaged.
- Durability: With few moving parts and robust construction, slewing drives are built to withstand harsh operating conditions, including extreme temperatures, heavy loads, and outdoor environments. Many slewing drives are sealed and lubricated for long-lasting use, reducing wear and tear.
Types of Slewing Ring Drives
- Worm Gear Slewing Drives: Worm gear drives use a worm mechanism to transfer torque and are known for their high load-carrying capacity and self-locking capabilities. They’re ideal for slow-speed, high-torque applications.
- Helical and Spur Gear Drives: These designs provide faster rotational speeds and are useful in applications that don’t require the self-locking feature but need efficiency and smooth operation.
- Dual-Axis Drives: For applications requiring movement on two axes (such as solar tracking systems that follow the sun’s path in two dimensions), dual-axis slewing drives are used to provide precision control in both horizontal and vertical directions.
Common Applications of Slewing Ring Drives
- Construction Machinery: In cranes, excavators, and drilling rigs, slewing drives allow the entire structure to rotate smoothly, supporting the machinery’s operation in precise lifting, digging, and positioning tasks.
- Solar Tracking Systems: Slewing ring drives are widely used in solar panels and heliostats to enable automatic, precise adjustments that track the sun’s movement, optimizing energy capture and efficiency.
- Wind Turbines: Slewing drives help control the pitch and yaw of turbine blades, adjusting them for optimal performance as wind direction and speed change.
- Industrial Robotics: In robotics, slewing drives support the movement and positioning of robotic arms, allowing for highly precise and controlled rotational movement needed in manufacturing and automation.
- Defense and Surveillance: Slewing ring drives provide rotation and stability for military equipment, such as radar dishes, tank turrets, and surveillance cameras, where precision and durability are paramount.
- Material Handling Equipment: Forklifts, conveyor systems, and turntables use slewing drives to improve the movement and positioning of loads, enhancing efficiency in warehouses and production facilities.
Factors to Consider When Selecting a Slewing Ring Drive
Choosing the right slewing ring drive depends on several key factors:
- Load Capacity: Determine the maximum load the drive will need to handle, considering both static and dynamic loads. This includes understanding both the axial and radial forces it will encounter.
- Rotation Speed and Torque: Identify the desired speed of rotation and torque requirements. Worm gears are ideal for high-torque, low-speed applications, while spur or helical gears work well at higher speeds.
- Operating Environment: If the drive will be used outdoors or in a harsh environment, ensure it has adequate sealing and is constructed from materials that resist corrosion.
- Self-Locking Requirement: For applications that require stable positioning without constant motor engagement, a worm gear slewing drive may be ideal due to its self-locking properties.
- Maintenance and Lubrication: While slewing drives are designed for durability, some may require periodic maintenance. Choosing a model with a reliable lubrication system can reduce the frequency of service.
Conclusion
Slewing ring drives offer a powerful solution for applications requiring stable and precise rotational movement under heavy loads. With a compact and efficient design, they are adaptable to various fields, from construction and energy to robotics and defense. By selecting the right type and size of slewing drive, operators can improve the performance, longevity, and efficiency of their equipment. Whether for high-torque applications or high-speed rotation, slewing ring drives are indispensable in modern machinery and technology.